Cheap PriceList for STEEL BLOCK Wholesale to Uruguay
Short Description:
Length max. 6.000 mm Width max. 1.800 mm Thickness max. 1.000 mm (in case of smaller thickness greater length and width) Weight max. 30.000 kg
Cheap PriceList for STEEL BLOCK Wholesale to Uruguay Detail:
Length | max. 6.000 mm |
---|---|
Width | max. 1.800 mm |
Thickness | max. 1.000 mm (in case of smaller thickness greater length and width) |
Weight | max. 30.000 kg |
Product detail pictures:
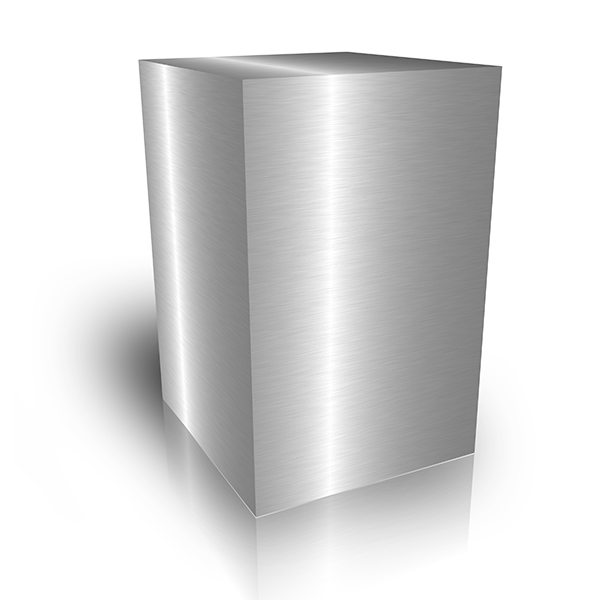
Cheap PriceList for STEEL BLOCK Wholesale to Uruguay, The product will supply to all over the world, such as: , , ,
TURN UP THE VOLUME!!! WATCH IN HD1080!!!!!!!
Student-made “I beams” being tested at RMIT University. April 30th, 2013.
Hello, this is one of my engineering videos, please enjoy. =D
=======================================================
We were given 2 metal sheets and had to build a beam from them. The best design would win. We had what we thought was “the best design” but we could not actually build the beam properly. Thus, it failed short of what we expected.
We made this beam using the machines at RMIT University.
Please do not copy our design, as we put a lot of effort into it, and it didn’t even achieve the highest score. Plus it is our work, copying it is Plagiarism. The testing machine broke half way through the testing of the other beams, so the force we obtained could even be wrong.
1st Song ~ Kingdom Hearts meets Metal – Eric
www.youtube.com/331Erock
2nd Song ~ Dialga Pokemon Theme Remix – The Pokemon Remix Studio
www.youtube.com/pokemonremixstuido
=============================
Detailed analysis of failure
=============================
The beam failed in compression on its top flange, as expected. It was able to obtain an ultimate limit state of 7.67kN, and an arguable service limit state of 2.3kN.
The main areas where the beam failed are immediately in the middle, and between the first major gap of rivets. We used 50 rivets in total. It is interesting that the beam deformed so much in the centre, despite the close location of the stiffeners. You may notice that there are 2 holes in the centre of the beam, these are not failed rivets. In production there was a miscalculation of the placement of rivets, so they were removed from the centre of the beam.
There was significant deflection in the major gap between the rivets as seen in the pictures. This is most likely due to the fact that the rivets were not put in properly in the first place. Before testing, in construction, the beam’s top flange was not properly constrained. So when the rivets were put in, there was already some small deflection in the top flange. The graph shows that there are 2 main points of plastic deformation on the beam. The first part represents the deformation of the middle, and the deformation after the ULS is from the rivets.
The linear region of the graph is actually between the 2kN and 6.5kN region. This means that the beam’s design is quite strong, but that the manufacturing was just faulty. And this is true. In construction one side of the beam had been made different from the other. Had they been the same, a higher result could have been achieved.
The bottom flange of the beam was fine during testing and is still in perfect condition. It was by far the best and most efficient part of the beam. It performed the strongly under the tension it was in.
To improve on the beam’s current design, the rivets would have to be spaced more evenly between the middle half of the beam. This would greatly enhance the beam’s stability, SLS and ULS. The middle stiffeners could also be moved closer to the centre to ensure less deformation earlier on. Basically we would have to improve the top flange’s capacity to take a compressive load without failure. If we could do this, our beam would have significantly higher serviceability and strength.
It should also be noticed that the testing machine began to be faulty and stopped working halfway through the tests. Therefore, we cannot fully trust all of these results.
Maximum deflection recorded in testing was 7.7mm. Maximum deflection recorded after testing was 10mm in the centre and 5mm in the mid-span of the top flange.
Group members: Amir, Dean, Stewart, George

